The Plan-Do-Check-Act (PDCA) Cycle, Explained (+Mind Map Examples of PDCA)
Mar 14, 2023
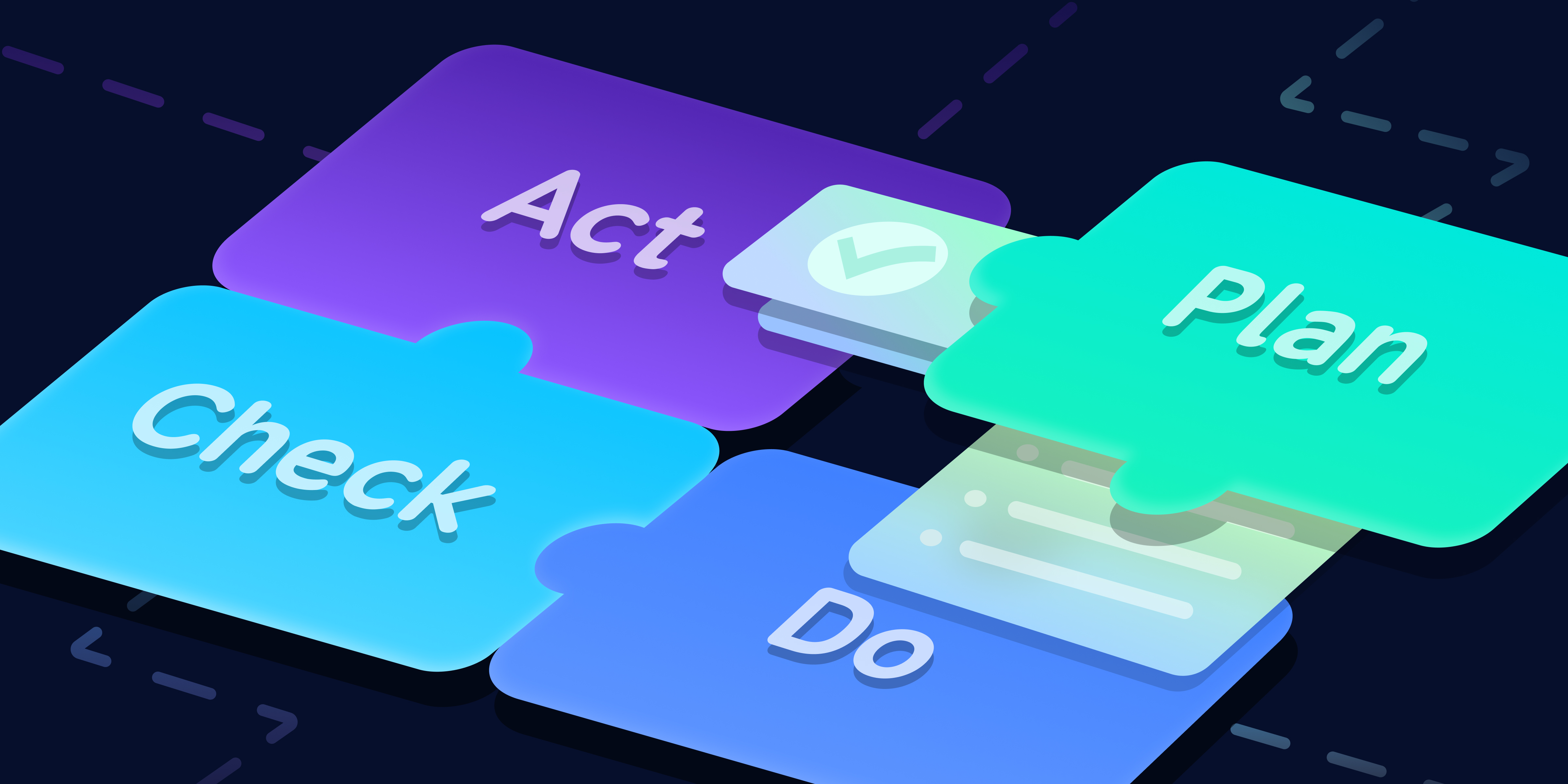
The Plan-Do-Check-Act (PDCA) Cycle, Explained (+Mind Map Examples of PDCA)
Mar 14, 2023
Are you tired of repeating the same mistakes over and over again? Do you want to improve your processes and achieve better results? Then PDCA is the solution for you! With its simple yet effective methodology, PDCA helps you identify problems, develop and implement solutions, and continuously improve your processes over time. By following this cycle, you can be an expert at solving problems.
What is PDCA?
PDCA was developed by Dr. W. Edwards Deming, an American statistician and quality management expert, in the 1950s. Deming's work focused on helping companies improve their production processes and achieve better results. He believed that quality was a key driver of success and that it could only be achieved through a continuous improvement process.
PDCA is based on the scientific method of problem-solving, which involves developing a hypothesis, testing it, and refining it until a solution is found. Deming saw that this same process could be applied to business and production processes, and thus PDCA was born.
The process of solving problems using the PDCA cycle is based on the scientific method. It involves planning an experiment to test a hypothesis, executing the experiment, studying the results, and using that information to form new hypotheses. This cycle is iterative, meaning that it is a continuous process that should never stop. Once an experiment is completed, the focus should shift towards planning the next one to continue moving towards improvement.
The beauty of the PDCA cycle lies in its simplicity and its effectiveness. By following this process, organizations can achieve continuous improvement in their processes and operations, leading to better quality, increased efficiency, and greater customer satisfaction. This cycle emphasizes the importance of being proactive, rather than reactive, in problem-solving and encourages a mindset of continuous improvement.
The PDCA model
Plan
The Plan phase is the first step in the PDCA cycle, and it involves identifying a problem or opportunity for improvement and developing a plan to address it.
- Identify the problem involves defining the problem, determining its scope and impact, and understanding its root cause.
- Establish goals involves setting specific, measurable goals that align with the organization's overall objectives.
- Develop a plan involves outlining a detailed plan for achieving the established goals. The plan should include specific actions, timelines, and responsibilities for each step.
- Define metrics involves establishing metrics to measure progress towards the goals and determine whether the plan is working as intended.
- Get buy-in involves gaining support from stakeholders and getting their agreement to move forward with the plan.
Do
The Do phase is the second step in the PDCA cycle, and it involves implementing the plan developed in the Plan phase.
- Implement the plan involves carrying out the plan developed in the Plan phase, including all of the specific actions, timelines, and responsibilities outlined in the plan.
- Collect data involves gathering data on the results of the plan. This may involve collecting quantitative data, such as production metrics or customer feedback, as well as qualitative data, such as employee feedback or observations.
- Document the process involves documenting the process used to implement the plan, including any deviations from the plan and any unexpected outcomes or issues that arose.
- Address issues involves addressing any issues or problems that arose during the implementation process. This may involve making adjustments to the plan, refining processes, or providing additional training to employees.
Check
The Check phase is the third step in the PDCA cycle, and it involves analyzing the data collected in the Do phase to determine whether the plan is working as intended.
- Analyze data involves examining the data collected in the Do phase to determine whether the plan is achieving the desired outcomes. This may involve using statistical analysis, qualitative analysis, or other methods to identify trends and patterns in the data.
- Compare results to goals involves comparing the results of the plan to the goals established in the Plan phase. This can help identify any areas where the plan is falling short and where improvements can be made.
- Identify deviations involves identifying any deviations from the plan that may have contributed to the results. This can help pinpoint areas where changes may be necessary to improve outcomes.
- Determine root cause involves identifying the root cause of any deviations or issues identified. This can help identify the underlying factors that are contributing to the problem and inform potential solutions.
Act
The Act phase is the fourth and final step in the PDCA cycle, and it involves implementing changes based on the insights gained from the Check phase.
- Develop an action plan involves developing a plan for implementing changes based on the insights gained from the Check phase. This plan should be detailed and include specific actions, timelines, and responsibilities.
- Implement changes involves carrying out the action plan developed in step 1. This may involve making changes to processes, procedures, or systems, as well as providing training or support to employees.
- Monitor results involves tracking the results of the changes made in step 2. This may involve collecting data on production metrics, customer feedback, or other relevant measures.
- Standardize the process involves standardizing the new process or procedure to ensure that it is followed consistently and that improvements are sustained over time.
Using Xmind to continuously improve
Xmind supports the conversion and mixing of different structures. When you need to clearly display all processes in the same diagram, you can use a mind map structure that links four tree tables . And based on this, you can continuously plan, do, check, and act.
You can even create a comprehensive tree diagram for all your PDCA, and mark each step as completed once it's done.
When should you use the PDCA process?
Using the PDCA cycle can be a game-changer for organizations that want to continuously improve and stay ahead of the curve. It's a flexible framework that allows for iterative problem-solving and empowers teams to adapt to changing circumstances. PDCA has become a widely accepted method for achieving continuous improvement in many areas of business and self-growth, including manufacturing, healthcare, and software development.
Achieving personal goals
For example, body weight management is a crucial part of personal growth, as maintaining a healthy weight can lead to numerous health benefits and improved overall well-being.
Enterprise management
Another example, manufacturing management is a critical component of business growth. Without it, companies may struggle to optimize their production processes, maintain high-quality standards, and meet the ever-changing demands of the market.
Last
Rome wasn't built in a day, and it's the same with becoming a pro in the workplace. But fear not, my friend! There's a handy tool called the PDCA model that can help you out. It's a loop process that you can use to keep improving and getting better and better. So let's jump on board and enjoy the benefits of efficient work together. Go, team!
Try Xmind Free